To see what I can do for you, click
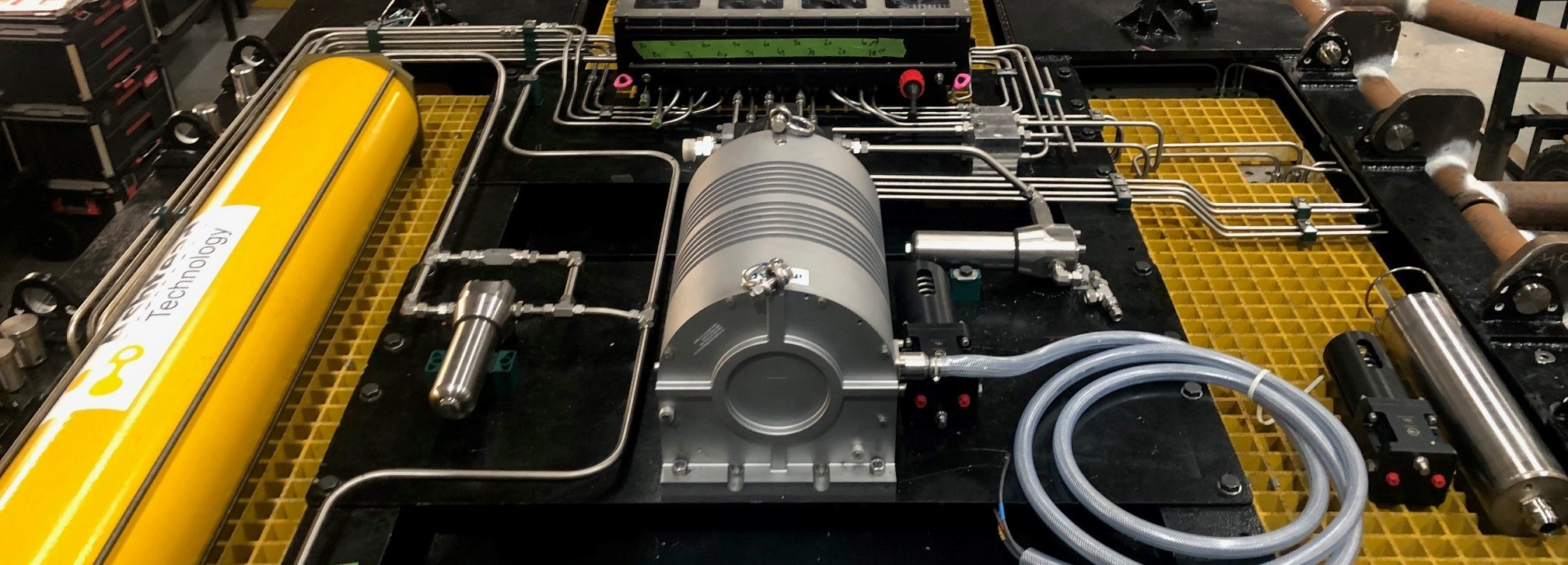
Mechanical and Electro/ Mechanical Design Engineering
Experience: I have been involved in all stages of the project lifecycle from initial concept through to final handover. This has included the creation of storyboards and renderings for customer approval; Research and Development; Product development using 2D and 3D CAD software; Production of fully detailed drawings and assemblies; Analysis (FEA); Liaising with sub-contractors and customers; Assembly management; Testing. I have also generated a wide range of technical documents including Design Descriptions, analysis documents and test procedures and reports. More on that in the Space Engineering section.
Capability: My experience working in Mechanical and Electro/ Mechanical Engineering is considerable, but working in the space industry took everything to another level. Not because the work is more technically advanced, but because everything is taken back to basics, and everything you do is questioned, then questioned again. Why did you choose this material? Will the motor still operate at -40 degrees C? Is there sufficient clamping force if the M6 screws are replaced by M5? If something breaks during launch, or while operating in space, you can't just go up and fix it!
Adaptability: Moving seamlessly from one industry to another, having had no prior experience, is something I am used to. Moving from one country to another, not knowing the language or governmental requirements, can be a challenge. I have now worked, and lived, in England (home country), Scotland, Spain, Austria, Norway, Belgium, Luxembourg and Malta. I have additionally worked in Denmark, Germany and China.
Industries: Each industry I have worked in has its own particular requirements, whether it's Military, Sub-sea, Space or Chemical, but if you have the experience and knowledge of engineering fundamentals such as material properties, manufacturing methods, and tolerancing, then these can easily be transferred from one industry to another. However, for the record, here is a selection from my list: Small arms; Flight simulators; Infra-red gas detector; Ship and submarine consoles; SatCom amplifiers; Waveguide; RF components; Radiation hardened shelters; Sonar; Lab robotics; Diesel Engines; Aircraft Engine; Cameras; Vacuum chambers; tractors; Automation; Sub-sea recovery; Sub-sea robots; Space optics; Space mechanisms.
Manufacturing techniques: Sheet metal; Castings; Steel structures; Welding; Precision machining; Extrusions; Plastic injection moulding; Vac-forming; Composites.
Environments: Explosive; Vacuum; Severe vibration; Shock; Rapid decompression; Thermal cycling; Marine.
Software: 3D: SolidWorks; AutoCad Inventor; Siemens NX; Pro/Engineer Wildfire; TurboCad. - 2D: AutoCad. - Additional software: SolidWorks Simulation; Inventor Nastran; FEMAP, Flowtherm; Pro/NC; Vault; PDM; MRP; Visual Studio.
Analysis: Modal; Vibration; Stress; Static and Dynamic Thermal
Testing: Vibration; Shock; Thermo Vacuum; Friction; Quasi-static.
Management: At the age of 25, I was supervising on-site installations. From then, I held the position of Team Leader, Design Manager at two companies, Principal Engineer at two companies, Project manager and Systems Manager. These positions were all technical. I was also joint owner of a large bathroom business, dealing with customer sales, bathroom design, purchasing, inventory control, accounting and project management.
Additional: RF ('C', 'X', 'Ku', 'Ka' bands, 40GHz); EMC; Electronics; Software. I also helped with the renovation of a property in Spain, where I was initially responsible for the purchase of the property, and then for the purchasing of raw materials, as well as assisting with the building work. Due to the location of the property, I had to learn basic Spanish very quickly.
I have an excellent understanding of tolerancing (GD+T), but more importantly, where critical tolerances should and should not be used because tolerances cost money as well as saving it. I always consider my designs with respect to manufacturability, assembly and use.
Download a copy of my resumé here. Back to top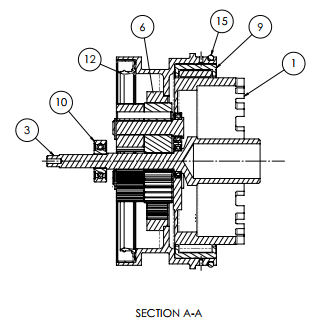
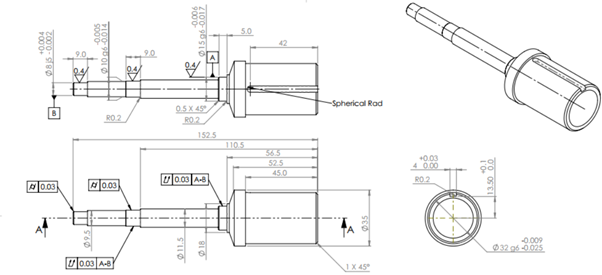
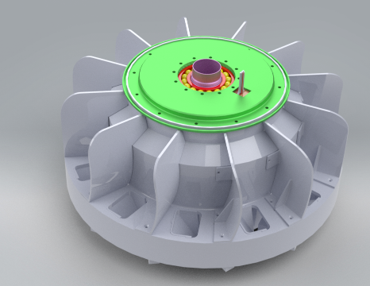
Space System Engineering
The Systems manager in the space industry works alongside the project manager, responsible for the technical side of the project while the Project manager deals with the finances and various customer issues.
The first task is to generate the Verification control document (VCD) which will list all of the technical requirements for the project, and will cross-reference to the documents which qualify the requirements. One of the systems managers tasks is also to determine feasibility of the requirements.
The next task is to ensure all members of the team are aware of the requirements that they have to satisfy. The Design Description (DDF) and Design Justification (DJF) documents are produced along with a Test Plan (TPL). Once the team is happy with the initial designs, a Preliminary Design Review (PDR) is held with the customer. This gives everyone the opportunity to review the design and make necessary changes.
Once PDR has been passed, 3D models and drawings are finalised along with an ICD, modal and stress analasis reports (ARP) and Test Procedures (TPR). A Critical Design Review (CDR) is held with the customer to review the final design.
Once CDR has been approved, manufacturing can commence. Close attention is made to material traceability and tolerance conformance.
During assembly, some testing can be performed such as friction for bearings, and fastener loading. Once the complete assembly has been built, a Pre-Test REview (PTR) is held with the customer to review the assembly and check test procedures.
Testing is rigorous. There are two methods for achieving space-flight qualification. One is to use an Engineering Qualification Model (EQM), where an identical unit to the Flight Model (FM) is tested to higher levels and timescales than the real levels, and then the FM is tested to the real levels and results compared. The other method is to use the ProtFlight method (PFM) in which a single unit is tested to the higher EQM levels, but at the shorter FM timescales. This unit then becomes the FM.
Once testing is complete, and assuming everything passes, the the Final Report (FR) is generated which details all the testing and results, and any deviations to the initial requirements that have customer approval. Space-Flight Qualification can then be given. The next thing you know, the hardware you worked on is on the launch pad waiting to be launched, and you are hoping that you made all the right decisions!
Nothing can compare to watching your first launch that you have been involved with, especially when so much dedication has been put in to the project. I worked as Systems Manager on Sentinel 1a and 1b, Sentinel 3a and 3b, and a GSTP, and as space mechanisms specialist on ExoMars and Solar Orbiter. I became the department vibration and shock specialist and we designed and built our own ringing-plate shock table.
Download a copy of my space resumé here. Back to top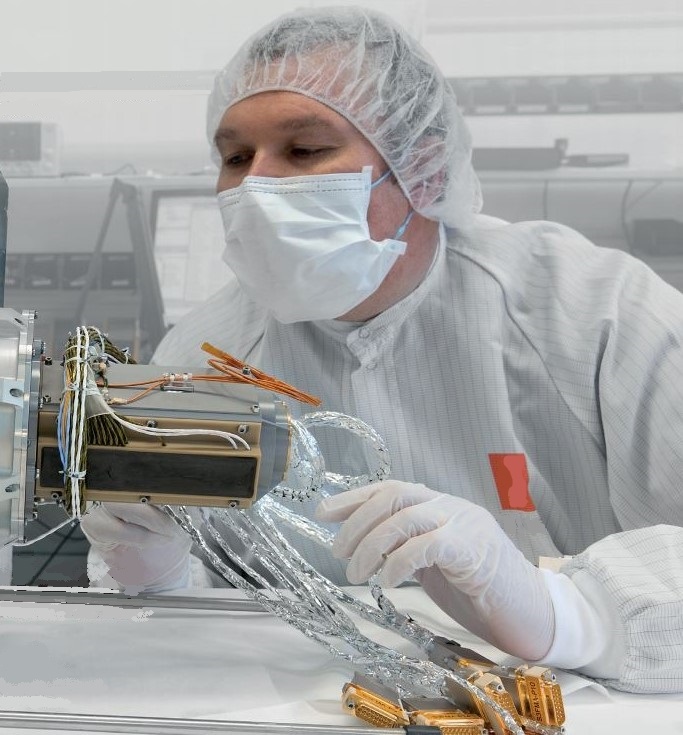
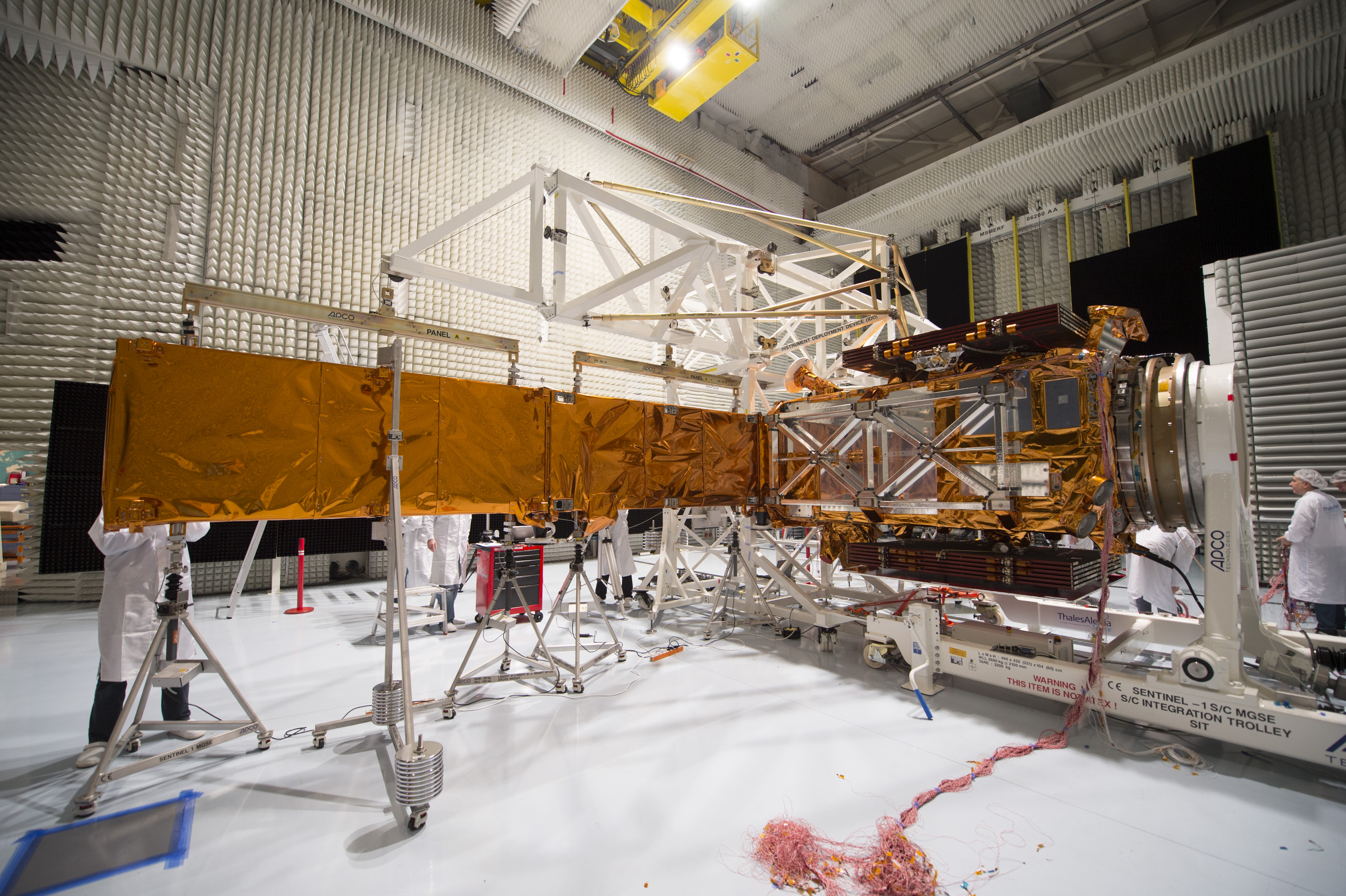